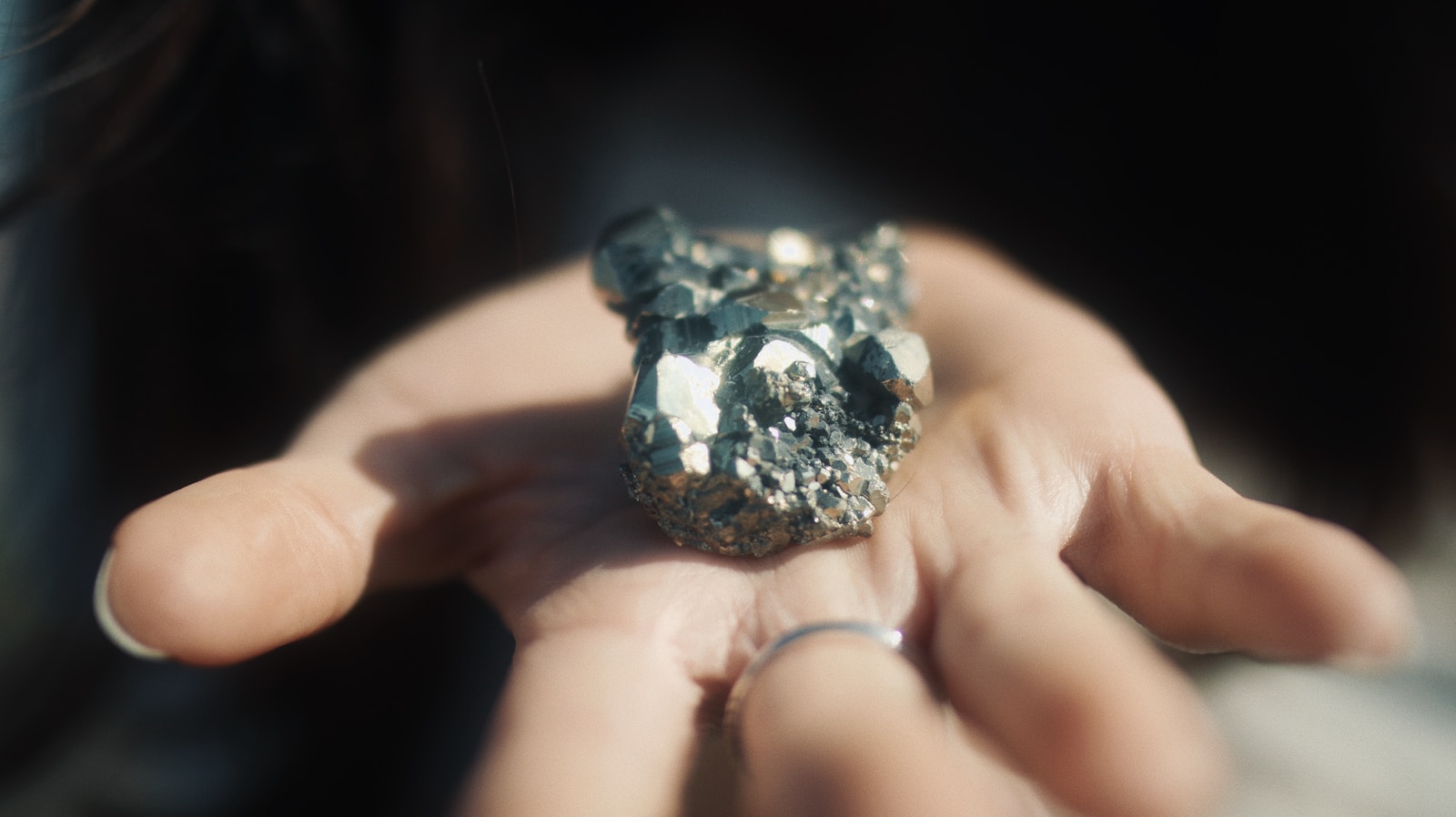
As a society, we are now well-versed in the benefits of recycling in our own homes – everything from food waste to glass, paper to tin cans. However, recycling is also taking place in the electronics industry, and on an industrial, rather than domestic, scale.
We are, of course, many decades into the ubiquitous use of electronics, and the role that everything from mobile phones to PCs play in our everyday lives. We have all, no doubt, lived through several laptops, and many phones; indeed, over two billion such devices will be sold around the world this year. However, each electronic device has a natural lifecycle and the question then becomes… what next? Once the family laptop finally gives up the ghost, what happens to it? This is electronic waste – sometimes referred to as e-waste – and you may already know that all these discarded devices contain ‘rare earth’ materials, specifically within their permanent magnets. While much of the device might be relatively worthless, the electronics industry relies on these special magnets and there is, therefore, value in extracting them from our electronic devices. Once removed, they can then be recycled and repurposed for use in industries including defence, transport and clean energy.
Up until now, there has been no process for doing this on an industrial, commercial scale. However, a project that started as an academic chemistry study in America in 2013 was upscaled by the country’s Department of Energy this year, resulting in an extraction process that can now retrieve 97% of rare earth materials from domestic electronic devices, such as hard drives.
70% of the magnet in such electronics is iron, which is not a rare earth material, so this new patented process uses nitric acid to dissolve the waste magnets, resulting in a solution that is then fed through a polymer membrane to separate the rare earth elements from the iron. That solution is then processed again, to create an oxide rich in rare earth material, now completely free of the iron. This material can then be recycled and used to make new magnets, driving everything from electric cars to wind turbines. As this process also creates less waste, there are other additional environmental benefits to this process.
Now proven to work, the US Department of Energy is focusing on upscaling the project, collaborating with industry to develop further commercial utilities. The ultimate ambition from a governmental and environmental point of view is to retrieve hundreds of kilograms of rare earth materials monthly, and ultimately be able to match manufacture with new rare earth materials, with those from this recycled process.
And there are other potential avenues for development. One possible off-shoot might be in filtering out other useful materials, such as cobalt and lithium. We have seen, for instance, the incredible evolution of electric cars, and that brings with it a commensurate need for lithium-ion batteries. It would be a fantastic achievement to imagine such environmentally-friendly, electronic vehicles built themselves, initially, with recycled batteries.
An awareness of where the raw materials that go into our electronics come from will benefit us as a community of electronic product designers and as a society as a whole. We will continue to monitor developments in electronic recycling technology and at Hi5 Electronics, we remain optimistic about the future.